Why Training is Hot at Fluid Handling
Do you need to increase your knowledge of steam or hydronic technology? Fluid Handling can help you with all your training needs.
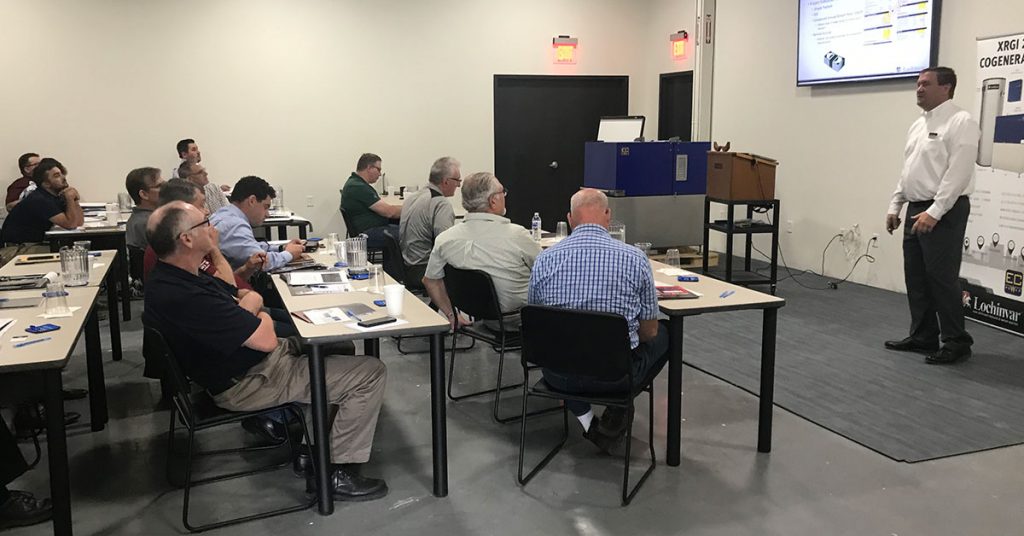
We’ve been helping consulting engineers, contractors, industrial plant managers and heating wholesalers expand their knowledge of steam and hydronic components, technologies and systems for over 30 years. A familiar face to anyone who has participated in one of our many training sessions during the last three decades is our training manager, Bill Armstrong.
He has a bachelor’s degree in industrial engineering from Iowa State University and a master’s in engineering management from the Milwaukee School of Engineering (MSOE). Much of his early career was spent working for Trane Corporation in engineering sales. He also worked for several years as an independent sales rep.
Armstrong joined Fluid Handling as a partner in 1984. He took over the training role at Fluid Handling in 1990. Soon after, in 1994, the company built a state-of-the-art training facility. Called the Fluid Handling Institute, it was housed in an addition to our building and included a 1,600-foot classroom with tiered seating and operating steam and hydronic displays.
With Fluid Handling’s move to a new facility in Menomonee Falls in the fall of 2018 and a rebadging of our logo, we now refer to our brand-new training room and class options as the FH Institute. The first class in our new classroom was August 21, 2019.
Training is a key priority for Fluid Handling. Historically, Armstrong wrote a lot of the training material and presented many of the programs. In recent years, we have expanded our list of trainers to include other internal experts.
“We’re fortunate to have some of the most knowledgeable steam and hydronic experts in Wisconsin on our staff,” Armstrong explains.
He emphasizes that the company has always taken a hands-on approach, not only teaching how systems work and how to design and size components for them but also how to troubleshoot them. “We don’t do commercials for the products we carry. We’re very careful to provide as much value to our students as we can.”
We also offer in-house training put on by some of our principal suppliers. “Those classes are product-specific and are also geared to be educational to systems as much as possible,” he points out.
Who gets trained in FH Institute classes?
Newer engineers to the industry need the practical, industry-specific knowledge that colleges can’t provide. More experienced engineers often like to know about trends in product development from the manufacturers. FH Institute provides both. Our classes are structured to meet the students’ requirements for PDH’s (professional development hours).
The FH Institute also trains many contractors, who buy and install the equipment. Understanding how it all works together gives them greater confidence in what they’re buying. Many courses provide PDHs so tradespeople can maintain their accreditations.
We also train industrial plant managers and heating wholesalers. Some of the manufacturers we represent also send people to us for training. Their engineers understand their products, but not how they work within a system. We give them that perspective.
Armstrong estimates FH Institute trains about 150 people per year at our in-house training facility. We train many more via online classes.
Correspondence courses increase FH Institute’s reach
FH Institute’s correspondence courses are delivered via email. Students receive messages with links to download the documents containing the course materials. They also receive tests via email, and they can contact the instructor to ask questions as needed.
This format is especially popular with customers who work in northern Wisconsin and other remote parts of our territory. They can’t justify driving to Milwaukee for a half-day class but can still benefit from these courses.
We also do video courses and webinars.
Hands-on learning provides a lot of value
Over the years, training has become integrated into many parts of our operations. For example, we use mobile displays in trailers to take our classes on the road and to do demonstrations at many locations around our territory.
In addition, our sales and service representatives make the most of “teachable moments” when they’re at a customer’s site, helping them troubleshoot and fix their systems.
“When you’re facing a problem system with a customer, you have the opportunity to ask certain questions that will help you to provide a solution to the problem,” Armstrong explains. “That allows the customer to learn by participating in the information-gathering process. It may not be classroom training, but it’s an important form of education that our customers tell us they really appreciate.”
Learning from failures
Over the years, Fluid Handling has collected a “house of horrors” – products that were misapplied and failed, sometimes spectacularly.
“We’ve seen a lot. We tell these horror stories during our classes to help students understand what can happen when you ignore basic principles of working with steam and hot water systems,” Armstrong recalls. “Our goal is to educate our customers and help them avoid expensive mistakes.”
“Our goal is to educate our customers and help them avoid expensive mistakes.”
– Bill Armstrong
For more information about the FH Institute and to register for upcoming classes, check out our classes page.